Dibujo Técnico: Tolerancias y Ajustes
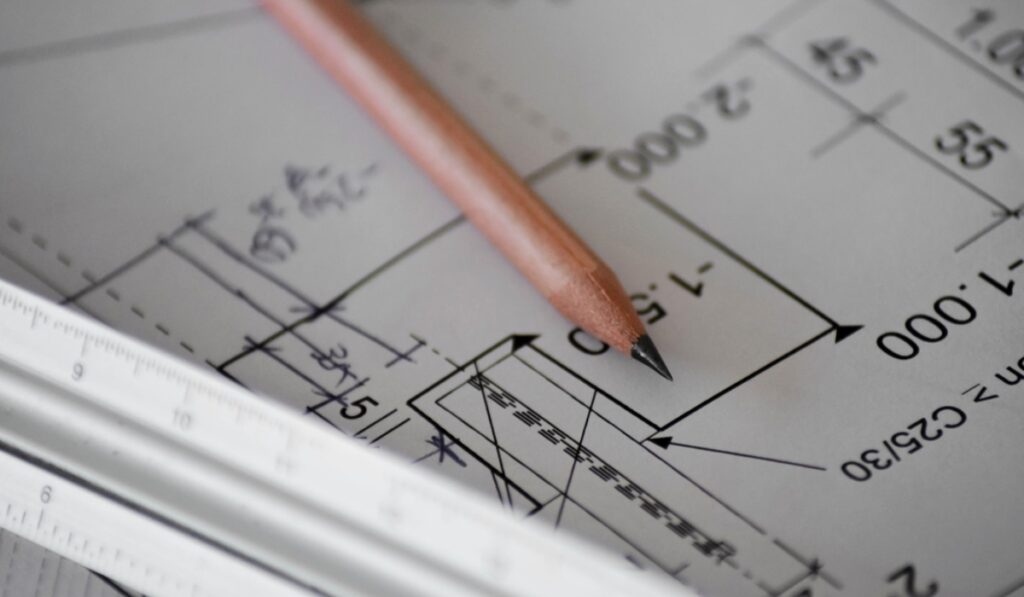
Tolerancias dimensionales
Tolerancia: cantidad total que se permite variar en la fabricación de una pieza respecto de lo indicado en el plano; definiremos pues, Tolerancia dimensional a la cantidad total que es permitido variar en la fabricación, a una dimensión especificada en el plano según la cota nominal.
Términos empleados en tolerancias
•Cota nominal. Es la medida indicada en el plano como básica e identificativa.
•Medida máxima. Es la medida máxima admisible.
•Medida mínima. Es la medida mínima admisible.a
•Tolerancia ( t ). Es la diferencia entre las medidas máxima y mínima de un elemento. Esta tolerancia puede situarse de las siguientes formas respecto de la medida nominal ( línea de referencia ) :
Encima ( + ): 50 (+30, +20 µm) t = 30 - 20 = 10 µm Dmáx = 50.030 mm Dmín = 50.020 mm
Debajo ( - ): 50 (-30, -20 µm) t = 30 - 20 = 10 µm Dmáx = 49.980 mm Dmín = 49.970 mm
Repartido ( ± ): 50 (+30, -20 µm) t = 30 - (-20) = 50 µm Dmáx = 50.030 mm Dmín = 49.980 mm
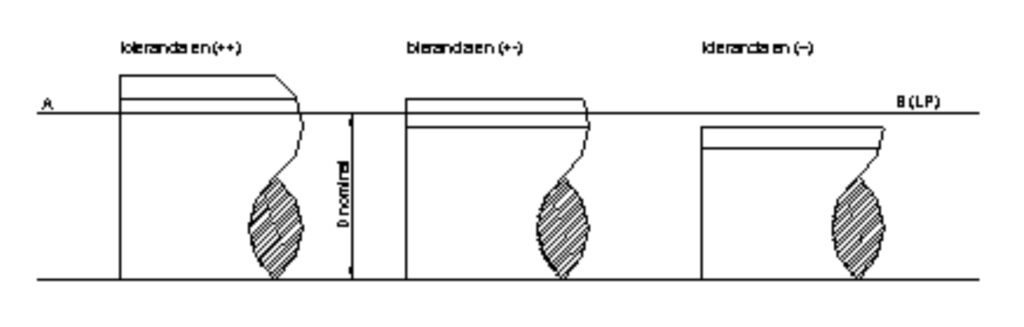
Ajuste. Es el acoplamiento entre varias piezas de la misma medida nominal.
Eje. Es la pieza que presenta contactos externos en un ajuste, es decir, es la parte contenida.
Agujero. Es la pieza que presenta contactos internos en un ajuste, es decir, es la parte continente.
Diferencia superior. Es la diferencia entre la medida máxima y la nominal.
Diferencia inferior. Es la diferencia entre la medida mínima y la nominal.
Diferencia de referencia. Es la que se utiliza para posicionar la zona de tolerancia, se toma la menor de la superior o inferior.
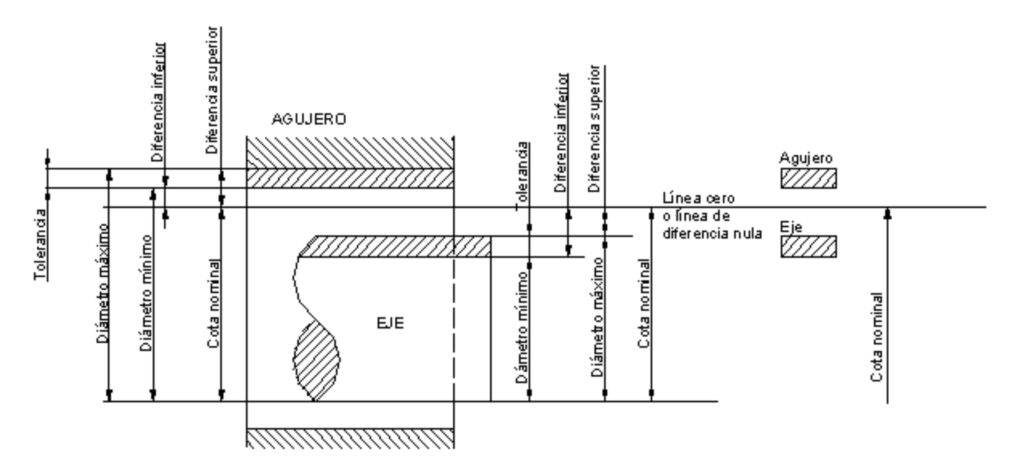
Tolerancias ISO
ISO ha normalizado un sistema de tolerancias que estudia los dimensionamientos hasta 500mm ( existen normas especiales para dimensiones superiores ). Este sistema utiliza unos códigos ( letras y números ) que definen la calidad de la tolerancia así como su posición respecto de la línea de referencia.
Por ej.: 50H7 = 50 (+25, 0 µm)
En este punto cabría destacar que las unidades empleadas son :
- mm para las medidas nominales.
- milésimas para las tolerancias.
Calidad de tolerancia: podemos decir que cuanto mayor sea la calidad menor será la tolerancia. El sistema ISO prevé 18 calidades designadas por : IT01, IT-0,...., IT-16,
Como aplicaciones generales podríamos citar las siguientes:
CALIDADES | APLICACIONES |
IT-01 - IT-5 | Construcción de instrumentos de control y en mecánica de alta precisión. |
IT-6 - IT-11 | En mecánica de precisión y para ajuste mecánicos en general. |
IT-12 -IT-16 | En trabajos de fabricación basta y piezas como de fundición, forja, etc. |
CALIDADES | 01 1 2 3 4 | 5 6 7 8 9 10 11 | 12 13 14 15 16 |
Campo de aplicación | Calidades y piezas de gran precisión. Elementos de control para procesos de fabricación (calibres y galgas). | Piezas mecanizadas y ajustadas para construcción de máquinas industriales. | Tolerancias de acabado para piezas no ajustadas. Piezas en bruto, laminadas, estiradas, forjadas o fundidas. |
Amplitud de la zona de tolerancia
A mayor calidad menor será la tolerancia admisible; por otro lado la experiencia demuestra que es mas fácil obtener una tolerancia de 5µm en un diámetro de 50mm que en uno de 400mm. De donde se deduce que la amplitud de la zona de tolerancia dependerá de :
- La calidad que se asigne
- Dimensión a obtener
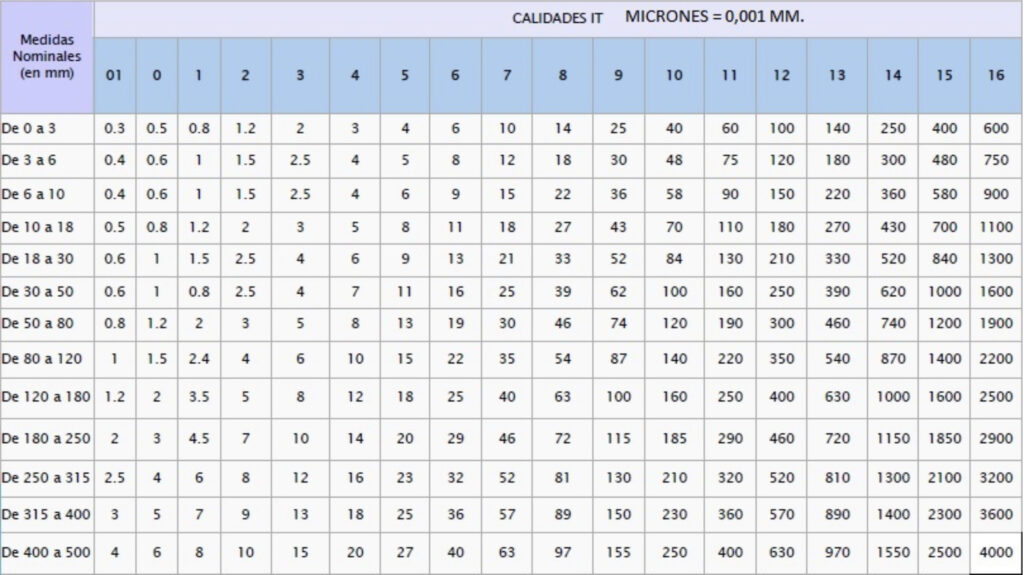
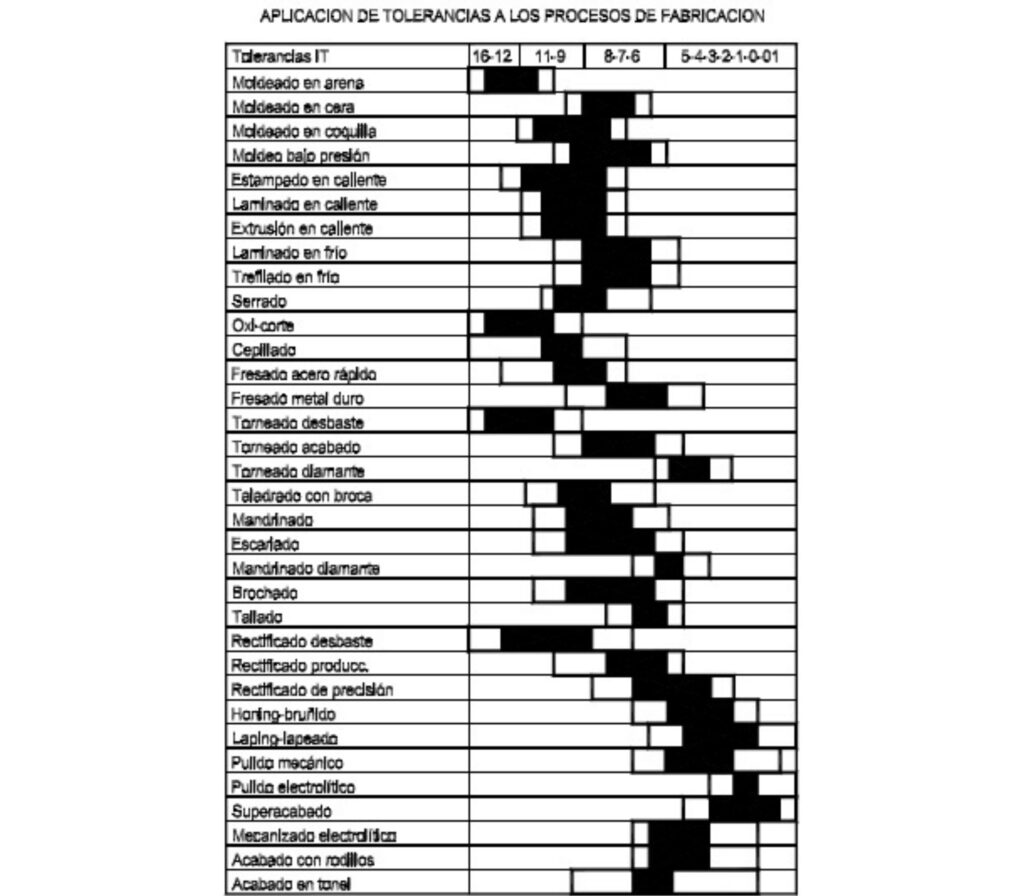
Posición de tolerancia
La posición de las tolerancias se determina por la diferencia de referencia que será la superior o inferior según esté por debajo o por encima. Las distintas posiciones, que se establecen para cada grupo de dimensión, se designan mediante letras que serán mayúsculas para agujeros y minúsculas para ejes. El sistema ISO establece las secuencias de posiciones mostradas en la adelante.
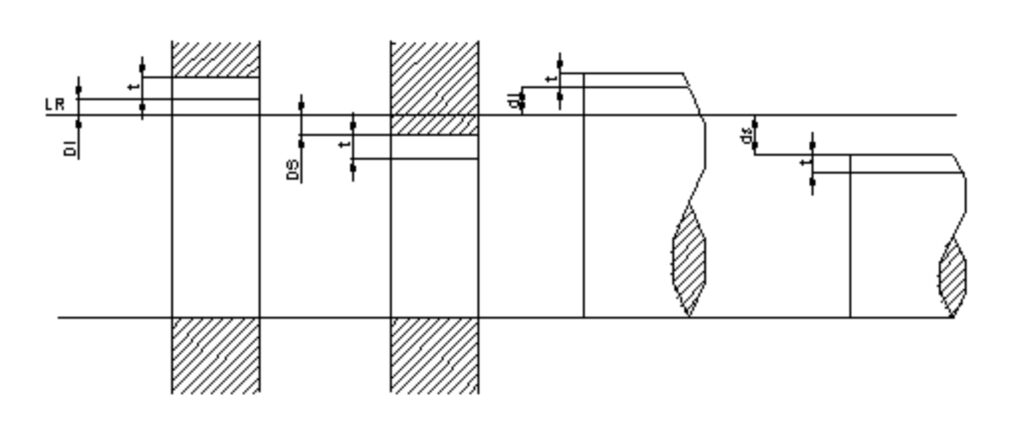
Características de las posiciones en los ejes
Las posiciones a, b, c, cd, d, e, ef, f, g, vienen fijadas por la diferencia superior que es negativa. Significan ejes con ajuste móvil.
La posición h proporciona una diferencia superior ds=0, y constituye la referencia más importante.
En las posiciones j, js la zona de tolerancia es atravesada por la linea de referencia. La posición js tiene la misma diferencia superior que inferior.
La posición k es una posición especial donde para determinadas calidades la diferencia inferior di=0 y para otras es positiva. Las posiciones m, n, p, r, s, t, u, v, x, y, z, za, zb, zc se fijan por la diferencia inferior que es siempre positiva. Estas letras significan ajuste fijo y a presión.
Características de las posiciones en los agujeros
Las posiciones A, B, C, CD, D, E, EF, F, G, vienen fijadas por la diferencia inferior que es positiva. Significan agujeros con ajuste móvil.
La posición H proporciona una diferencia inferior Di=0, y constituye la referencia más importante.
En las posiciones J,J s la zona de tolerancia es atravesada por la línea de referencia. La posición Js tiene la misma diferencia superior que inferior.
Las posiciones K, M, N pueden coincidir por encima o por debajo de la línea de referencia dependiendo de la calidad. Las posiciones P, R, S, T, U, V, X, Y, Z, ZA, ZB, ZC se fijan por la diferencia superior que es siempre negativa. Significan agujeros con ajustes fijos y a presión.
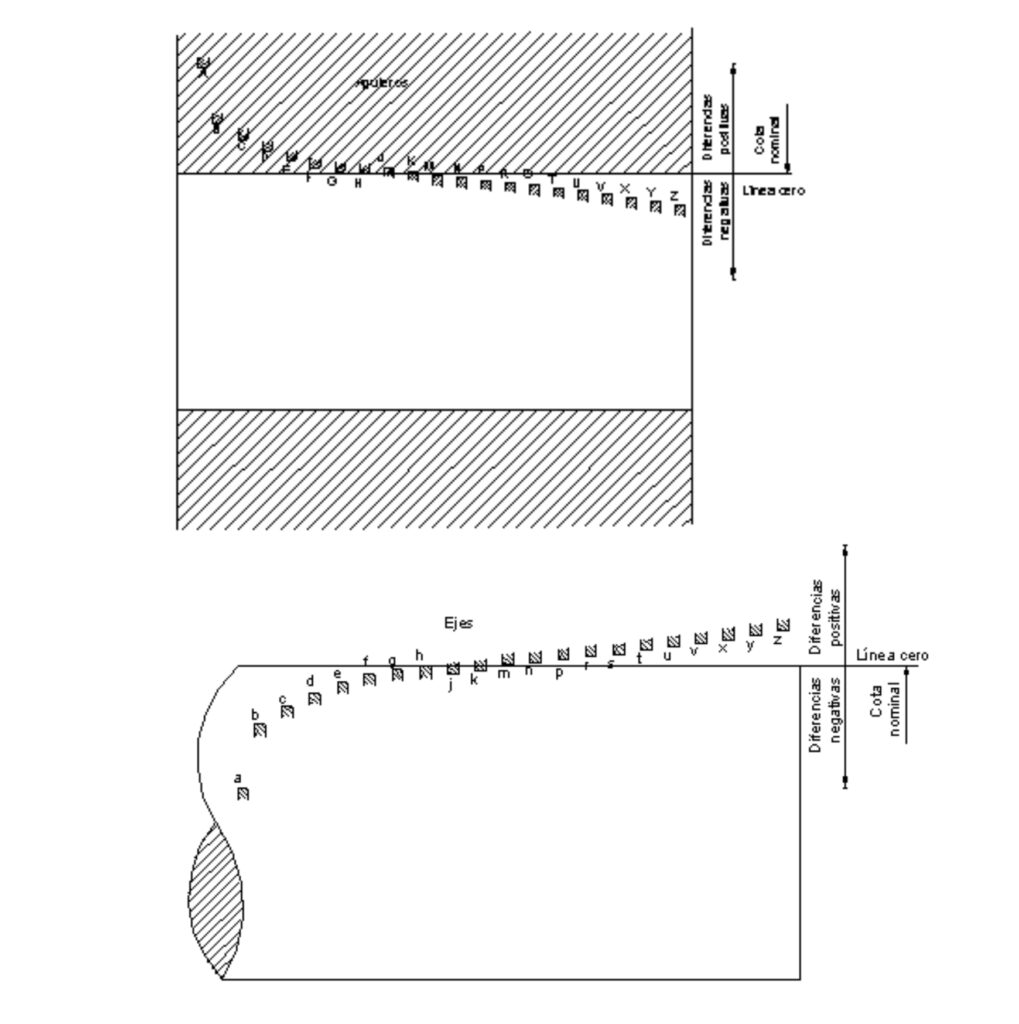
Determinación de la diferencia de referencia
El sistema de tolerancia ISO, define unas tablas en las que se determinan las diferencias superior e inferior que servirán para determinar la diferencia de referencia. Se muestra a continuación un extracto de las tablas con las posiciones más utilizadas en mecánica general.
La distancia de referencia depende de :
- Calidad de la tolerancia
- Dimensión de la pieza
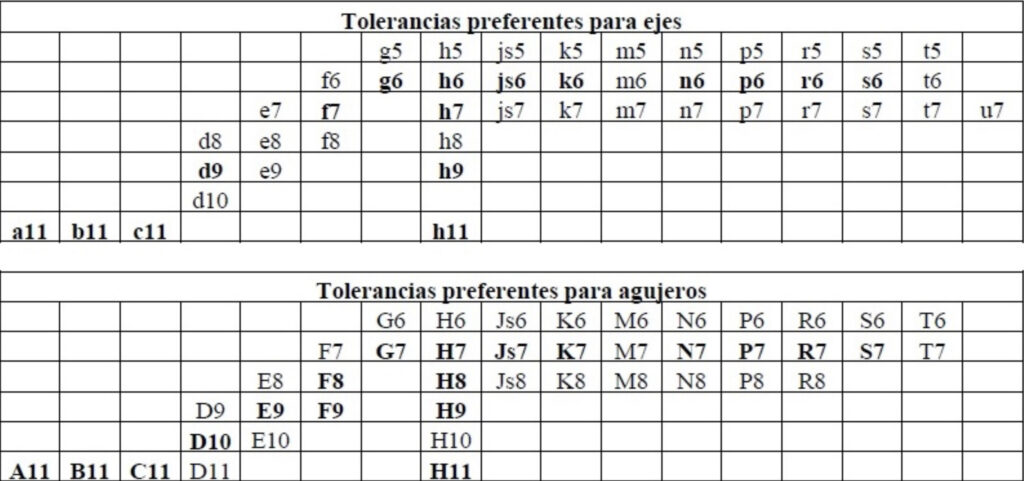
Diferencias superior e inferior para ejes

Diferencias superior e inferior para agujeros
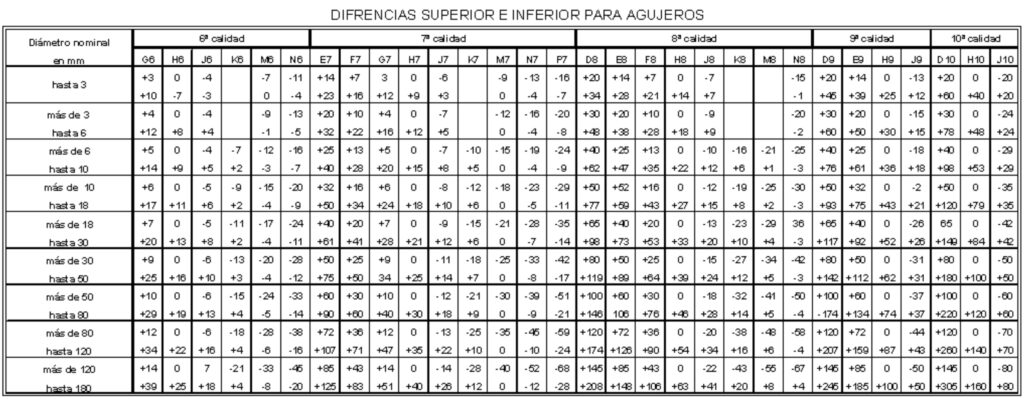
Ajustes
Juego máximo. Es la diferencia entre la medida máxima del agujero y la mínima del eje (Jmáx = Dmáx - dmin).
Juego mínimo. Es la diferencia entre la medida mínima del agujero y la máxima del eje (Jmín = Dmín - dmax).
Apriete máximo. Es la diferencia entre la medida máxima del eje y la mínima del agujero (Amáx = dmáx - Dmin).
Apriete mínimo. Es la diferencia entre la medida mínima del eje y la máxima del agujero (Amin = dmin - Dmáx).
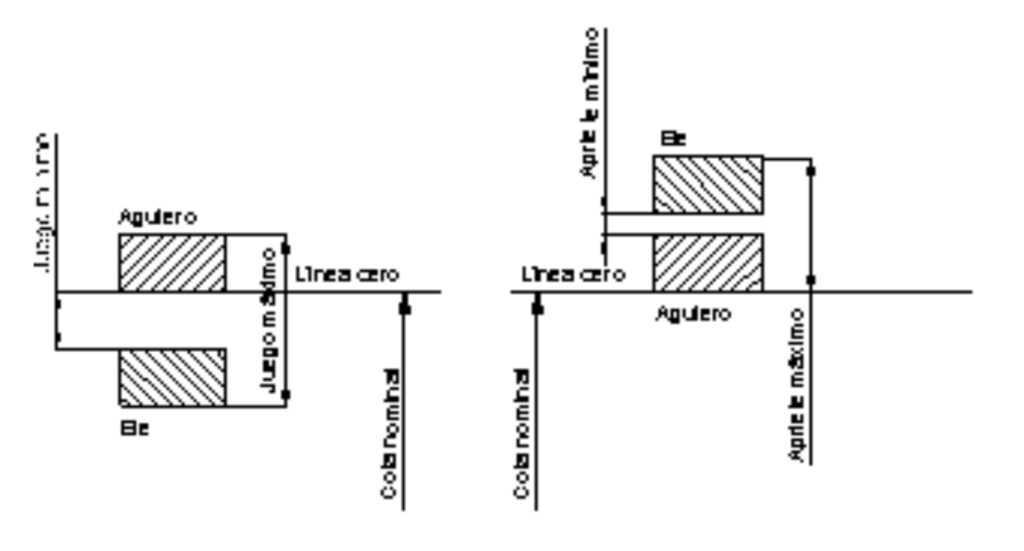
Tipos de ajuste
El sistema ISO prevé tres tipos de ajustes:
Ajustes móviles. En los que las partes consideradas presentan cierto juego u holgura por lo que las partes son móviles una respecto de la otra. Se dan cuando el Jmáx sea (+) y el Jmin sea (+).
Ajustes fijos. Se presenta apriete durante el montaje y una vez efectuado resulta un ajuste más o menos apretado. Se dan cuando el Amáx sea (+) y el Amin sea (+).
Ajuste indeterminado. En los que las partes consideradas pueden presentar juego o apriete. Se dan cuando el Jmáx sea (+) y el Jmin sea (-).
Métodos para montar y desmontar piezas con ajustes a presión

Medios de calentamiento de rodamientos
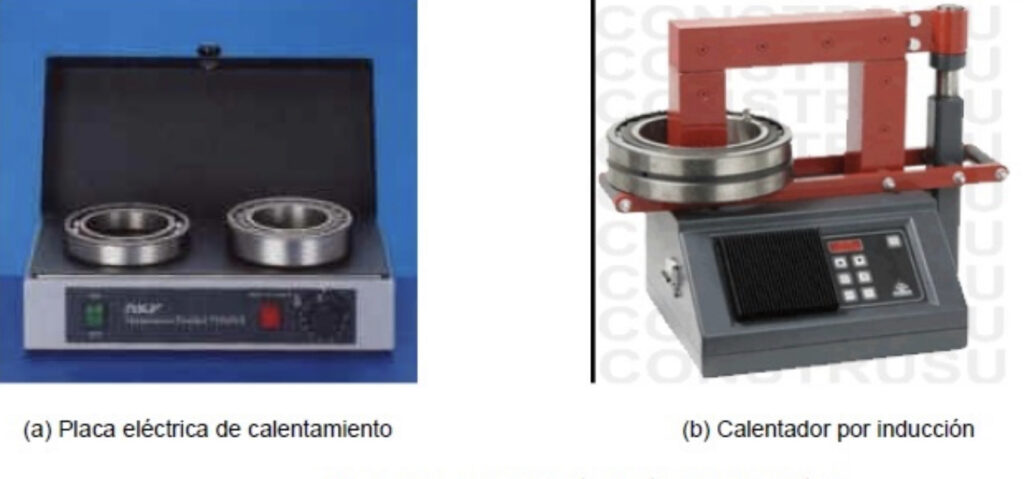
Sistemas de Ajustes ISO
Estos sistemas tienen por objeto fijar el conjunto de tolerancias a emplear en los ajustes, ya que hay que tener en cuenta el gran abanico de posibilidades que se presentan en las combinaciones de 28 posiciones de tolerancia con 20 calidades distintas en 13 grupos de dimensiones para ejes y otro tanto para agujeros. Teniendo en cuenta esto, se han establecido dos sistemas fundamentales que ISO recomienda utilizar.
Sistema Agujero - base. (Agujero único)
Sistema Eje - base. (Eje único)
La utilización de dicho sistema de ajustes aporta una serie de ventajas, tales como:
- Independencia de la fabricación.
- Posibilidad de fabricación en serie.
- Intercambiabilidad.
Sistemas Agujero base
Este sistema contempla una posición para el agujero de forma que la diferencia inferior es nula, es decir se selecciona la posición H. Manteniendo fija esta posición, se obtienen ajustes fijos móviles o indeterminados jugando con la posición del eje.
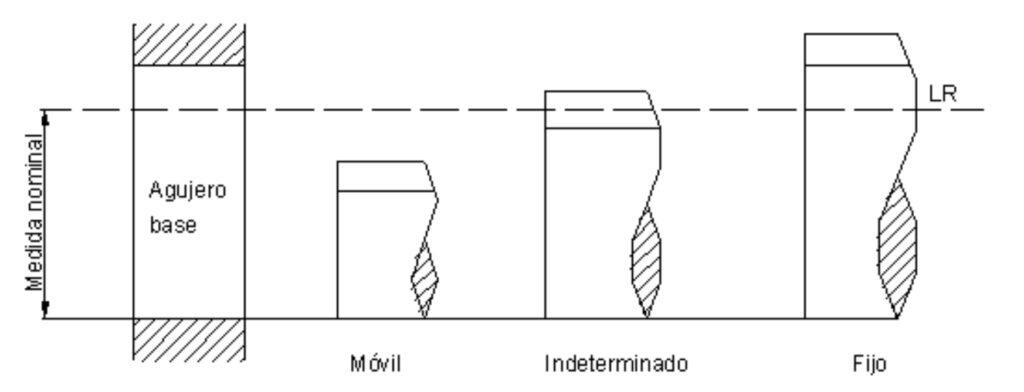
Se muestra a continuación los tipos de ajustes que se pueden obtener en función de las diferentes posiciones.
Posición del eje
a, b, c, cd, d, e, ef, f, g, h, j, js, k, m, n, p, r, s, t, u, v, x, y, z, za, zb
Resultado para posición H
Ajuste móvil
Ajuste indeterminado
Ajuste fijo
Sistemas Eje base
Este sistema contempla una posición para el eje de forma que la diferencia superior es nula, es decir se selecciona la posición h. Manteniendo fija esta posición, se obtienen ajustes fijos móviles o indeterminados jugando con la posición del agujero.
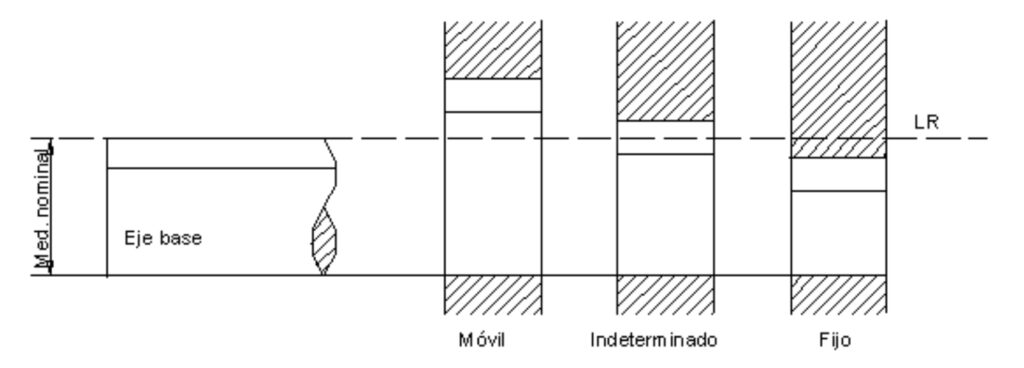
Se muestra a continuación los tipos de ajustes que se pueden obtener en función de las diferentes posiciones.
Posición del agujero
A, B, C, CD, D, E, EF, F, G, H, J, JS, K, M, N, P, R, S, T, U, V, X, Y, Z, ZA
Resultado para posición h
Ajuste móvil
Ajuste indeterminado
Ajuste fijo
Ajustes recomendados ISO
Al designar el acoplamiento de un ajuste se indicará siempre primero el agujero y después el eje.
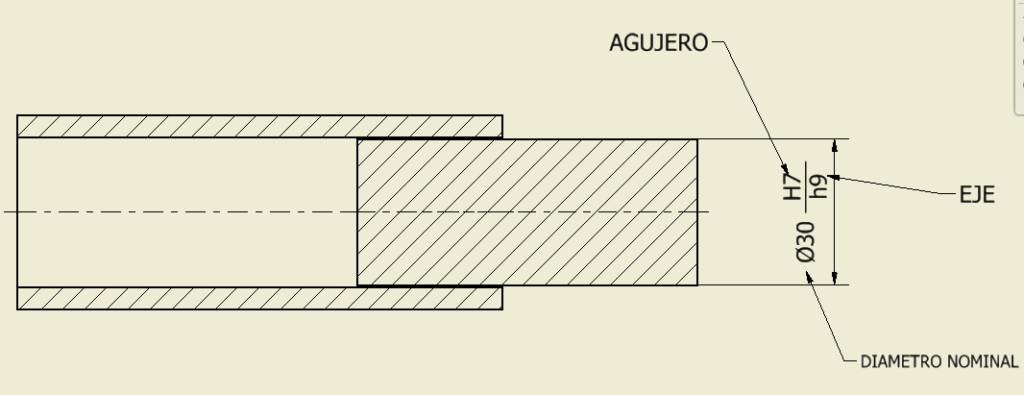
Formas aceptadas de acotación
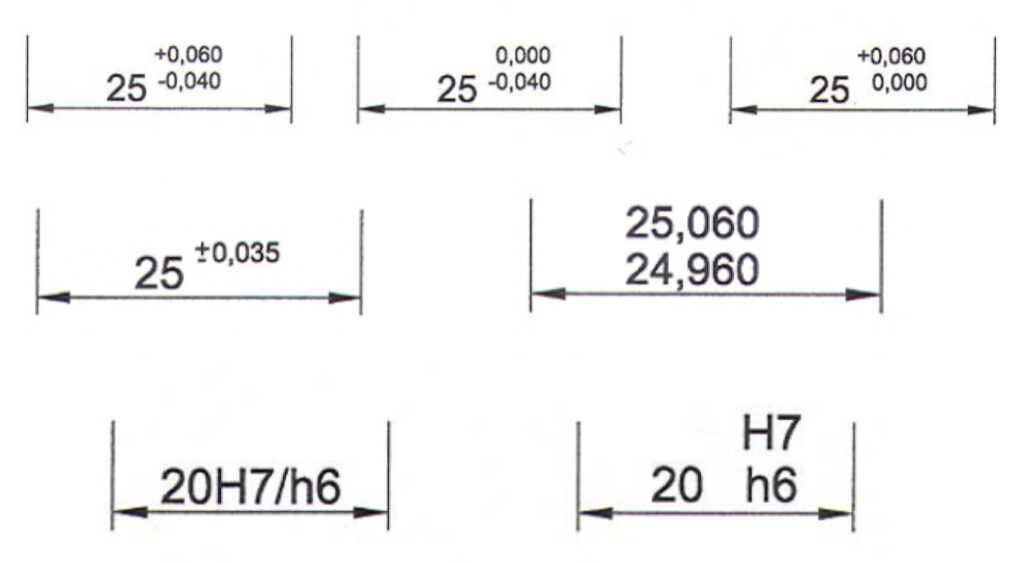
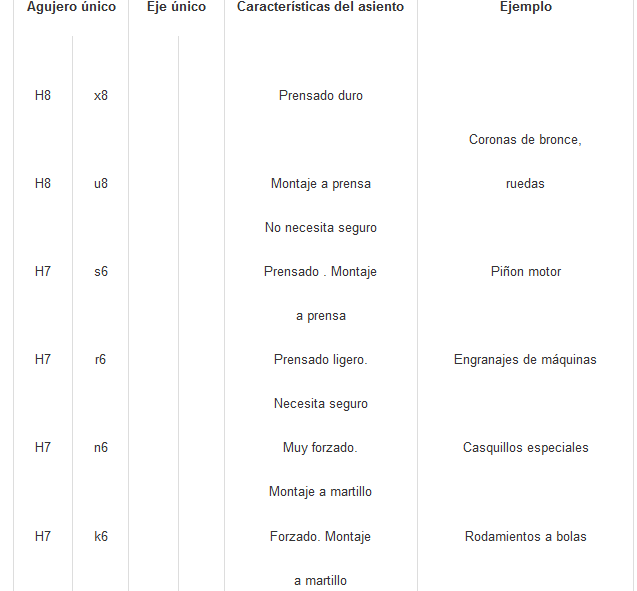
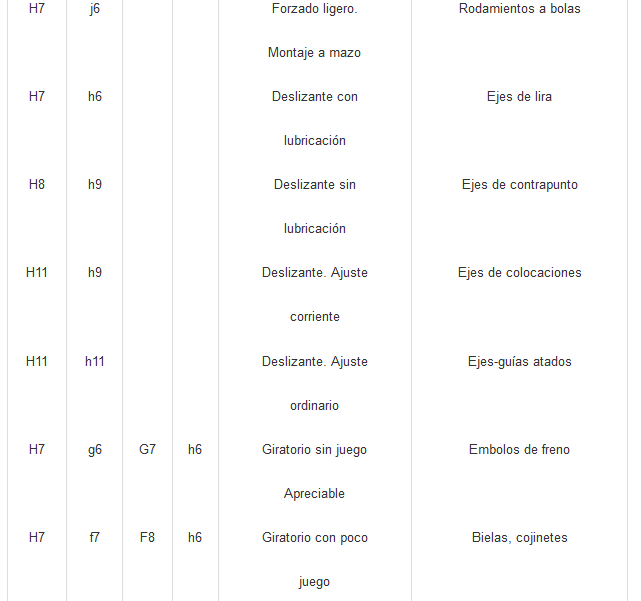
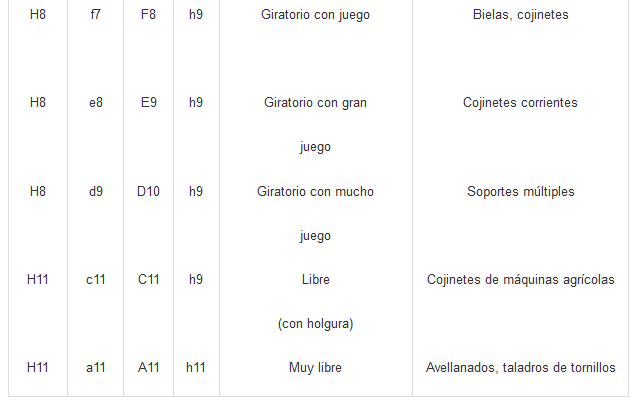
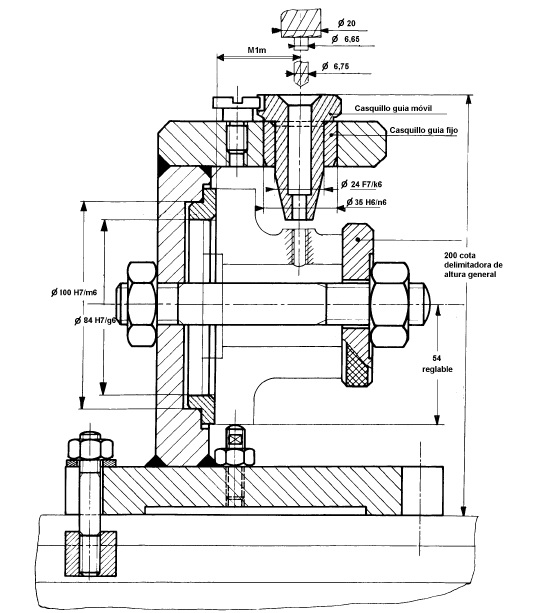
Si quieres conocer otros artículos parecidos a Dibujo Técnico: Tolerancias y Ajustes puedes visitar la categoría .
- Tolerancias dimensionales
- Términos empleados en tolerancias
- Tolerancias ISO
- Amplitud de la zona de tolerancia
- Posición de tolerancia
- Características de las posiciones en los ejes
- Características de las posiciones en los agujeros
- Determinación de la diferencia de referencia
- Diferencias superior e inferior para ejes
- Diferencias superior e inferior para agujeros
- Ajustes
- Sistemas de Ajustes ISO
- Sistemas Agujero base
- Sistemas Eje base
- Ajustes recomendados ISO
Deja una respuesta
También Puedes Leer